CONSUMPTION FOR UNLOADING
The three steam driven cargo oil pumps will consume about 3.6 tonnes fuel oil per hour.
Total consumption per 24 hours of full unloading capacity will be about 86.4 tonnes of fuel oil.
|
CONSUMPTION FOR LOADING
One electrical driven ballast pump will consume 0 08 tonnes of fuel
oil per hour One steam driven ballast pump will consume about 0.3
tonnes of fuel oil per hour.
Total consumption per 24 hours of full loading capacity will be about
9.0 tonnes of fuel oil.
|
CONSUMPTION FOR INERTING EMPTY SHIP
To inert the empty ship will take about 24 hours and it consumes
about 30 tonnes of fuel oil.
|
SLUDGE HANDLING DAVIT
Two(2) sets of portable air motor driven davit with capacity of 0.2
tonnes.
|
BALLAST SYSTEM
Segregated ballast tanks fulfilling Marpol 73/78 requirements as segregated tanker. The ballast water is discharged through overboard valve on ship's side or through bottom sea chest
|
BALLAST PUMPS AND EDUCTORS
One steam turbine driven, vertical centrifugal pump with a capacity
of 2,000 cu.m per hour at 30 mTH.
One set of electric motor driven, vertical centrifugal pump with a
capacity of 2,000 cu.m per hour at 30 mTH,
One water ballast stripping eductor with a capacity of 200 cu.m per
hour at 25 mTH.
>
|
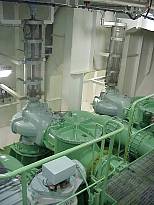
turbine and el motor driven ballast pumps
|
|
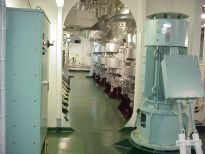
el motor and turbines to drive cargo and ballast pumps
|
 
CARGO SYSTEM
Twelve(12) cargo oil tanks, total capacity of cargo oil tanks is 166,383 cu m or 1.046.522 barrels at 98%.
Two(2) slop tanks fully coated with coal tar epoxy, total capacity of slop tanks is 3,880 cu.m or 24,402 barrels at 98%. Three grades of oil can be handled simultaneously with two valves segregation.
The cargo pumping system allows maximum unloading rate of 12,000 cu m per hour with three main cargo pumps. Vessel to allow a maximum loading rate of approximately 14,500 cu.m per hour through the cargo manifolds
|
PUMPS
Cargo oil pumps: Three(3), steam turbine driven, vertical centrifugal
pumps with a capacity of 4,000 cu.m per hour at 135 mTH each.
One(1) set reciprocating, stream driven, cargo oil stripping pump with a
capacity of 150 cu.m per hour at 135 mTH.
One(1) cargo oil stripping eductor, with a capacity of 300 cu.m per hour
at 25 mTH
|
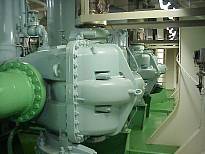
cargo oil pumps
|
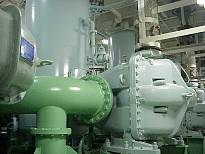
cargo oil pump
|
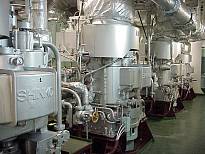
turbines to drive cargo oil pumps
|
 
|
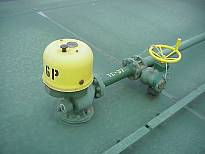
crude oil washing machine
|
TANK CLEANING EQUIPMENT, COW SYSTEM
Each cargo tank has two(2) deck mounted, programmable crude oil
washing machines with a capacity of 80 cu.m per hour at a thrust of 34
meters.
Maker: Consilium, Sweden
Type: 270ft Gun Clean
Each slop tank has one deck mounted, programmable crude oil
washing machine with a capacity of 80 cu.m per hour at a thrust of 34
meters and one set of bottom mounted, automatic programmed crude
oil washing machine with a capacity of 41 cu.m at a thrust of 18 meters.
Maker: Consilium. Sweden
Type Mini A Gun Clean
|
 
TANK GAUGING SYSTEM
Each cargo and slop tank is fitted with Saab tank radar level gauge
system with built in high/low level alarm, remote controlled from the
cargo control room
Each water ballast tank including peak tanks is fitted with Pan-Asia
electro-pneumatic type tank level gauge system with remote readout in
the cargo control room
|
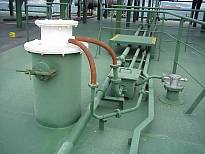
SAAB system radar
|
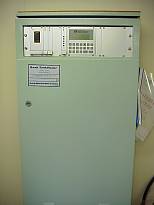
SAAB control cabinet
|
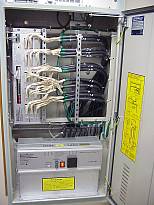
SAAB controle cabinet - inner side
|
 
VALVES
Valves in cargo oil and water ballast systems are of hydraulic remote
controlled type, operated from the cargo control room Blanks and
pressure testing arrangement fitted for seavalves and overboard
outlets.
Maker: Han-II
|
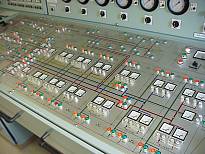
cargo control console
|
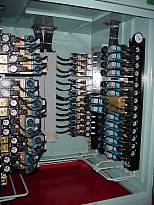
V/v cabinet for v/v remote control system
|
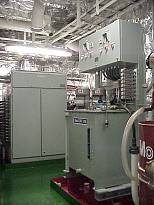
V/v cabinet and Power unit for v/v remote control system
|
 
GAS WARNING SYSTEMS
The fixed gas warning systems is continuously monitoring
hydrocarbon gases in pump room and ballast spaces and
02 + H2S in pump room, with safety fuctions relayed to bridge.
|
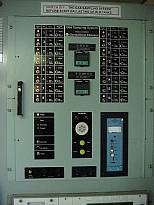
gas warning system – control console
|
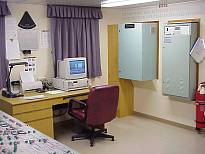
Loading computer; Gas warning system control cabinet; SAAB control cabinet
|
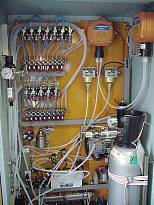
gas warning system - control cabinet (inner side)
|
 
LOADING COMPUTER
The loading computer is of "on-line" type and monitoring the level of
cargo oil tanks and water ballast tanks, and the draft by on-line
connection with tank gauging system and draft gauging system.
Maker: Kockumation AB
Type Loadmaster
|
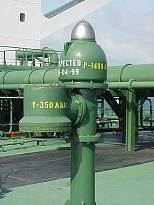
pressure / vacuum valve
|
HIGH VELOCITY VALVES
Press-Vac valves with double pressure outlets are fitted on cargo
and slop tanks including one common mast riser
Maker: Se-WonCo., Ltd.
|
 
INERT GAS SYSTEM
The inert gas system has a capacity of 15,000 cu.m per hour and is fed by two blowers, each holding 50% of the total capacity Maker: Alborg Sunrod kk
|
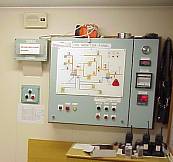
IG control console (cargo control room)
|
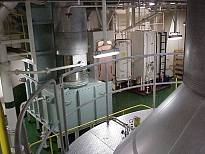
scrubber
|
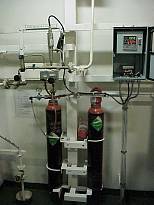
Oxygen analyzer
|
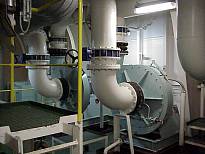
funs of IG system
|
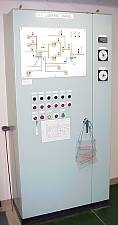
control board for IG system (ECR)
|
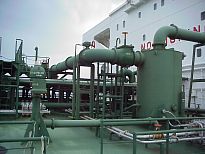
water deck seal
|
 
VAPOUR LOCKS
Calibrated vapour locks fitted to perform complete closed loading,
ullaging and sampling if required.
|
 
|

tank gauging system monitor; gas warning system; OIL POLLUTION MONITOR 'SERES'
|
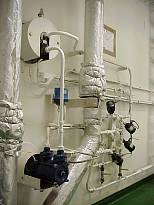
sampling pump and aux piping for
Oil Discharge Monitoring System
|
OIL POLLUTION MONITOR
For monitoring the discharge of oily water one oil discharge monitor
complying with MARPOL requirements is installed and controlled
from the cargo control room.
Maker: Seres, type S 663 MK lll III
|
 
MARINE SANITATION DEVICE
A sewage holding tank of vacuum type with a capacity of 5 cu.m
USCG approved, is installed
Maker: Evac
|
POSITION OF MANIFOLDS
- Centre of manifolds from midship of L 0 A - 0.75 m
- Distance from the foremost part of the ship
to the center of the manifolds - 135.34 m
- Distance from the after most part of the ship
to the center of the manifolds - 133.85 m
- Distance from manifold flanges to ship's side - 4.60 m
- Distance between manifold flanges - 1.69 m
- Distance between center manifold
and center manifold - 2.50 m
- Distance between manifold and roller bar - 4.30 m
- Distance between center of manifold
and main deck at side - 2.10 m
- Distance between center of manifold and keel - 26.52 m
- Distance between center of manifold and waterline,
normal ballast condition arrival - 17.91 m
|
 
CARGO HEATING SYSTEM
Heating coils are installed in all cargo and slop tanks, The heatng system is capable of raising the temperature in the cargo oil tanks from 44 °C to 66'C in 96 hours during voyage with ambient air temperature of 2'C and sea temperature of 5'C and of raising the oily water(50/50) temperature in the slop tank from 44'C to 66'C in 24 hours at the same conditions as above.
|
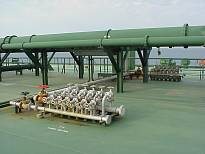
heating system one of tanks
|
CONSUMPTION FOR CARGO HEATING
A=ISO Standard i.e. air temp 25'C, sea water temp 25'C
B= Winter-Standard i.e. air temp 2'C sea water temp 5'C
To rise the cargo temp from 44'C to 66'C can be done in 96 hr,
the average fuel oil consumption for this will be 27 tonnes per
hour in case A(ISO-Standard), and 34 tonnes per hour in case
B(Winter-Standard). To maintain the cargo temperature at 135'F
will consume 1.1 tonnes per hour in case A(ISO-Standard) and 1.4
tonnes per hour in case B(Winter-Standard).
To maintain the cargo temperature at 100'F will consume 0.9
tonnes per hour in case A(ISO-Standard) and 1.1 tonnes per
hour in case B(Winter-Standard)
|